
"Los Marcianos"
Extraterrestrial habitation concept held by NASA
An AR/VR scene simulates two experimental 3D printing techniques using natural resources found directly on the planet's surface.
"Los Marcianos"
-- Extraterrestrial habitation concept held by NASA
Project NASA experimental 3D-Printed Mars Habitat Design
Teammate Nick Bruni, Xincheng Ye, Erik Sven Broberg
My Role Deployment Journey, modeling, simulate AR/VR scenarios in Unity, create illustrative diagrams.
Software Autodesk Maya, Rhinoceros, Grasshopper, 3ds Max, V-ray, Zbrush, Unity3d, Keyshot, Adobe Photoshop, Illustrator, After Effect
Instructor Guvenc Ozel, Benjamin Ennemoser & Mertcan Buyuksandalyac
Location NE Syrtis, Mars
Honor NEXTFEST17 Conference by FutureX, Los Angeles, US
The idea of colonizing another world has always been a fantasy of ours. It is in our nature to pioneer new lands to settle and inhabit even the most unforgiving environments. If NASA's astronauts ought to have a long-term presence on the moon or on Mars, they'll need to figure out ways to build habitable structures, something that will protect them from the extreme temperatures radiation and micrometeorites.
NASA's engineers face major challenges shipping large quantities of cement or other heavy raw building materials; sending them aboard rockets just isn't practical or cost-effective in the long run. Engineers at NASA's swamp works are developing a solution 3D printing habitats on other planets using natural resources found directly on the planet's surface.
For more background information: NASA & Autodesk experiments with 3D-printing robots to build habitats on other planets.
Presentation Equipments:
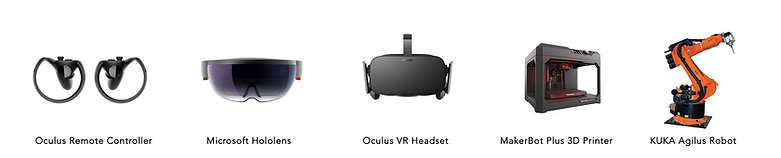
Problem Statement
How to build a habitable structure on Mars?
To fulfill the concept of a long-term Mars colonization mission, the GOALS of the explorers are:
-
Constructing an artificial environment and shielding from intense solar radiation.
-
Creating a livable climate, especially the right temperature in the right places.
-
Maintaining a pressurized enclosure at all times and protection from the toxic Martian atmosphere.
-
Reduce payload requirements for long-term habitation endeavors.
-
A garage for Mars Rovers (connecting or moving between separate structures).
-
Traverse and explore the outside world for scientific researches.
We will focus primarily on utilizing the planet’s weather conditions to harvest and store both energy and construction materials. We discovered what these materials are made of and realized how they could be utilized for the industrial construction of sustainable structures. So, where to begin the actual mission?
The first thing we need to do is to select the landing site and analyze its wind direction.
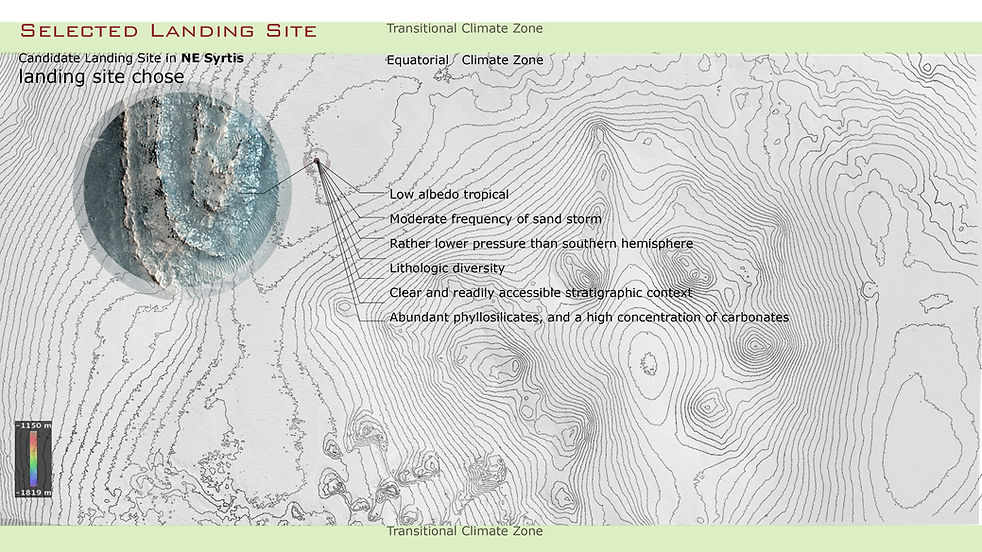
Wind Direction Analysis


Potential Solution
Autonomous fabrication
Key criteria we identified in this potential area are:
-
Located in the Equatorial Climate Zone which would have a moderate temperature.
-
Lithologic diversity potentially means a huge amount of construction materials.
-
Sandstorms frequently lift materials up in the air, so that we can maximize output while minimizing payload.
-
Abundant phyllosilicates, a high concentration of carbonates may offer basic life requirements.
Using new additive manufacturing technology, combined with the latest advancements in material science, structures can be sustainably built using a combination of local materials and lightweight recycled materials. By mixing small amounts of plastic waste with lunar or Martian regolith(similar to dirt and rock found in desert climates on earth), a cement-like structure can be formed and composited into place with robotic precision.
As previously touched upon, the colony will be constructed almost entirely autonomously and in two phases after a proper site is selected. Based on these initial ideas, this simple draft diagram showcases how the idea develops and how this journey will respectively solve the proposed problems.
Experimental 3D printing technique 1:
We intend to use sunlight and sand to achieve this process; the former is a virtually unlimited vast energy source, the latter is has an almost unlimited supply on Mars in the form of quartz. This process of converting a powdery substance via a heating method process into a solid form is known as sintering and in recent years has become a central process of designing prototype named SLS ( Selective Laser Sintering.)
.png)
Deployment Journey_mainSteps
Application:
Imagined Scenario
Once the mother spacecraft reaches Mars’ orbit, it will begin comprehensive storm surveillance over a variable period of time in order to optimize landing site selection. A large storm may need to be tracked and the spacecraft carrying the mesh will need to land before the storm arrives in order to deploy its mesh shell and achieve the following result. After a proper site has been selected, a cargo ship carrying the mesh and 3D printing equipment will land at the site.



Unfolding structure Mesh above the unfolding structure
It will immediately deploy the mesh via an accordion unfolding structure which was previously compacted in the belly of the cargo ship. This mesh will then perform the duties of melting the basalt/silica composite according to sensor density and wind directional constraints.
Shell Heating Activation Program

Our manufacturing process consists of harnessing common silica/basalt dust in storms in an effort to melt the material into a translucent and air-tight biosphere. This melting condition will propagate over an autonomously actuated tensile, mesh-shell which consists of multi-directional modules or panels. These are activated depending on wind direction and subsequently deactivated once a density threshold is achieved.
The attached video is an animation showcasing the process of air-tight biosphere generation.
Construction Process Simulation
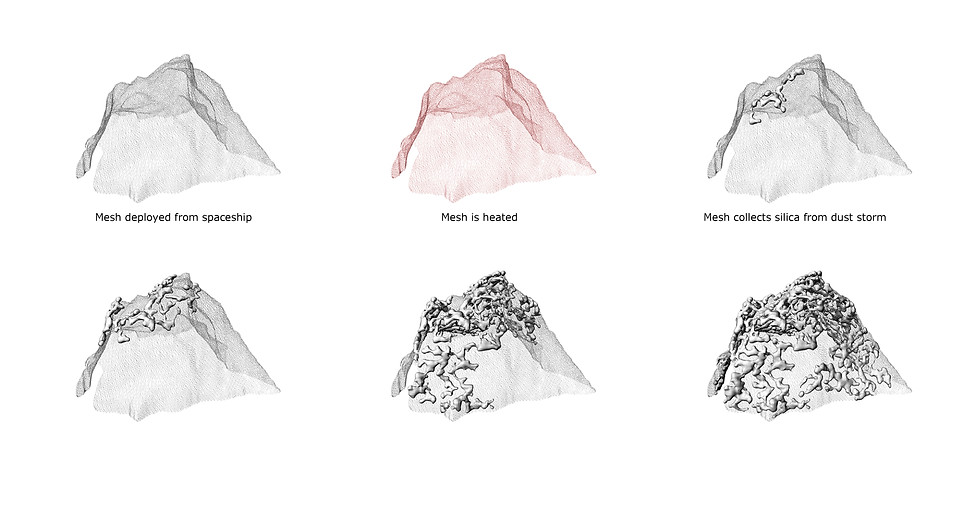

Prototype & Mockup
During the manual process, we simulated the process with fine sugar and laid brown and white sugar over the double mesh layers. Using a heat gun to reach the target temperature, the sugar became liquefied and then solidified into a translucent form when it cooled.
However, when it comes to doing the actual iterations, the heat gun would not accurately simulate the conditions. We leveraged the KUKA Robot Arm to build a larger scale mockup to simulate the generation of our air-tight biosphere. We replaced our materials with fine sand and glue spray and built several holders to grab and fix our tools into place while the robot arms are working. With the pre-programmed routines and the I/O controllers, the sand and glue went before and after on this hexagon structure overlapped with fine mesh which simulates the unfolding structure and its upper mesh (made by CNC Machine).
Small-scale Mockup of brown & white sugar Large-scale Mockup 30cm*30cm

Construction process in Robot Lab

Experimental 3d printing technique 2:
For the interior environment of the biosphere, we proposed the use of 3D printers hanging from specific nodes within the biosphere. They will print the interior form of the habitat with the same silica/basalt material into geometries catenary in nature.
Inspired by the Aerial Camera System in the sports game, we came up with the idea of the hanging printers because of the unfolded structure used to hold up the mesh. Its function is not only to fix and hold the upper mesh, but also provide inner pre-built tracks along each edge and cross. In response to joystick movements, the winches reel in and pay out the ropes, moving the printer up or down and side to side allowing for full range of motion within the enclosure.

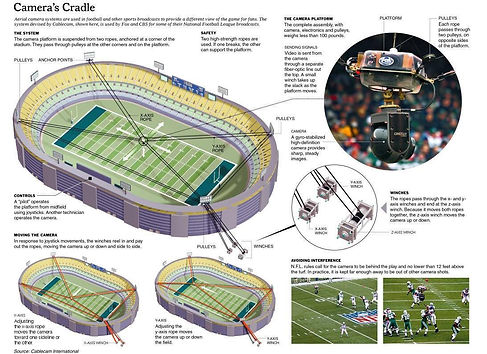
Prototype & Mockup
This unique 3D printer head is designed by our team to solve the problem specifically for such a situation. The hanging rope goes under the winches and equipped with motors that allow it to reel in or pay out the ropes to control the printing directions. There is a large silo to store sand in the middle of the device and one medal printing nozzle right underneath. Normally, the interactive screen is designed for workers to check out the printing processes or errors, nozzle conditions, and material inventories. But due to its autonomous requirements, this interactive screen cannot be manually commanded during the process, they will all be controlled remotely by the Mission Control Center (MCC).
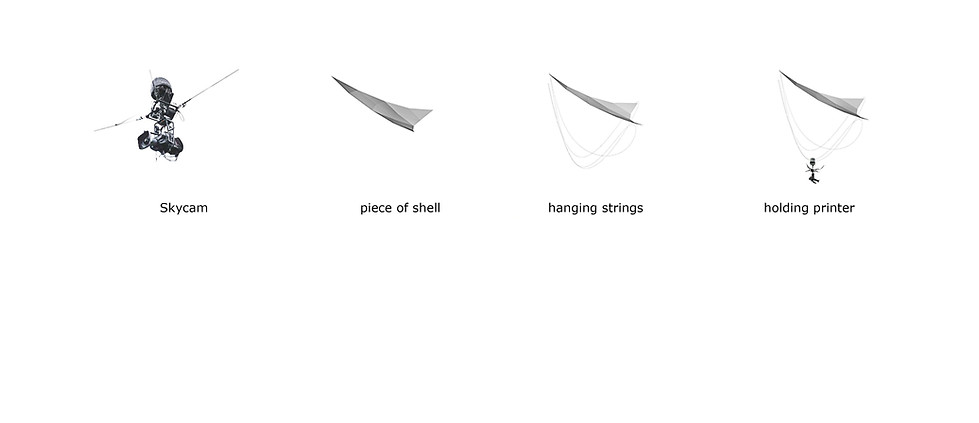

Printing Routine Information
The interior form of the habitat will be printed intermittently amid lulls and after the storm passes via a 3D printer suspended from the tracks within the structure of the mesh. This printing system will utilize the dust (which is partially stored in a large silo), to print highly accurate translucent interior enclosures. Incidentally, this printer will follow a natural catenary trajectory which will inform the forms printed into catenary hanging and vaulted structures.
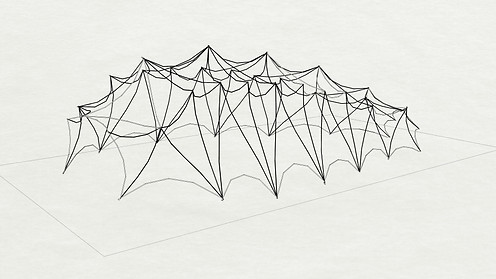


Deployment Sequence
To get the clear picture of the inner structure of this habitation, we made an explosion diagram to showcase all of the layers, from the outside to inside is melted regolith shell, heated aluminum mesh, tensile hexagon structure and the last is 3d printed habitat. The entire tent is connected with spaceship by Airlock.

Experience Design
In an idealistic sense, the site will not only contain sufficient dust storm activity to ensure total material propagation of the biosphere’s mesh shell but will also provide for periods of relief in order to allow autonomous vacuuming of the excess silica buildup from inside the biosphere. Furthermore, once the dust storm period terminates and an air-tight biosphere is realized, it will be optimal to have less storm activity to ensure safe human occupation within the site.




